Plastic Cores
10″ HIGH-RESOLUTION HMI
MINIMAL WASTE
MORE EFFICIENT
THAN CORE-JOINING
Automatic Core Cutter
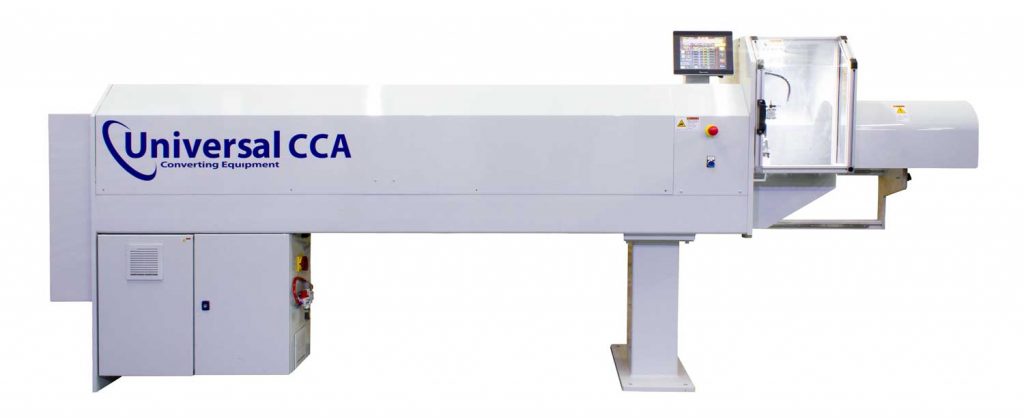
The CCA Automatic Core Cutter by Universal Converting Equipment is a cost-effective machine requiring minimal operator intervention. With a touch screen interface, operators can program various core lengths for each cut sequence to optimize parent core usage. The machine grips the parent core with a pneumatic actuated mechanical gripper, measures its length automatically, and begins the core cutting sequence. A servo positioning system advances the core under the knife, which can trim the edge if needed. The PLC-controlled system ensures precise cuts, allowing up to 7 different lengths to be programmed.
The CCA Automatic core cutter uses a pneumatically loaded knife, powered by a high-powered pneumatic cylinder, to cut through the hardest of core materials including cardboard, plastic and paper cores. The blade retracts automatically after each cut, extending its lifespan. Cut pressure is set via the touch screen, eliminating the need for manual adjustments.
Safe to Operate
The access door and main guard have safety switches to prevent the machine operating if either are open. The system is monitored using a dedicated safety relay. All moving parts are guarded.
Simple and intuitive operation
The machine is designed to be a cost effective unit requiring the minimum of operator intervention. The 9” colour touch screen interface allows the operator to program their required core lengths.
Extremely precise cut length control
The core is indexed forward to the new cut position using a high precision ball screw with servo control of the indexing. This allows movement to micron accuracy. Unlike belt driven systems, the accuracy does not diminish with time.
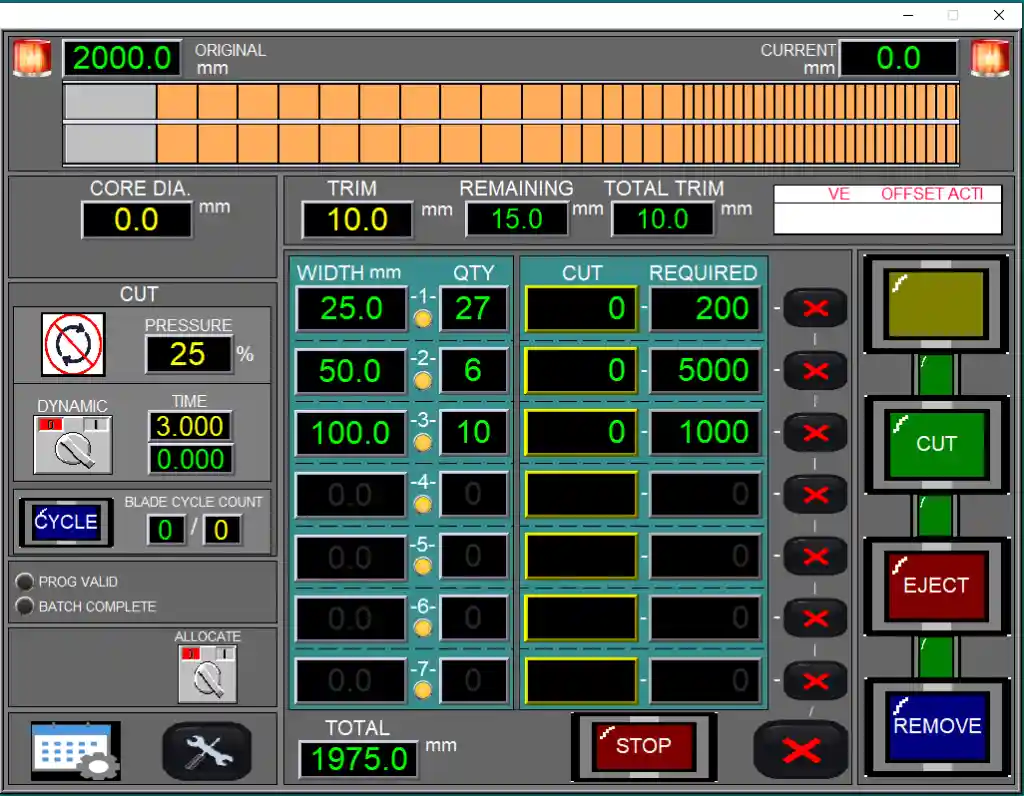
Robust Construction
The machine base is a fabricated steel structure that is very rigid. The machine is very strong and has been designed for a long life with the minimum of maintenance.
Automatic core length measurement
The core is drawn into the machine and the length of the core is measured automatically before the core cutting sequence begins.
Automatic speed setting to suit core outside diameter
Maximum cutting speed of 60 Cores per minute (Dependant on core material and cut width)
The speed of rotation is automatically set to keep the optimum surface speed to obtain a clean cut.
Automatic cut depth measurement
The machine senses when the blade has cut through the core and the blade is automatically retracted to maximise the blade life.
Automatic or programmable core trim function
The servo positioning system advances the core under the knife. If selected, an initial trim is taken to clean up the edge of the core, then the required core lengths are produced.
Core loading support
The machine has an adjustable core loading support to assist with loading the parent core into the machine.
Automatic core support height setting
The rollers that support the core during the cutting process are automatically positioned at the correct height to suit the core being processed. There are no adjustments for the operator.
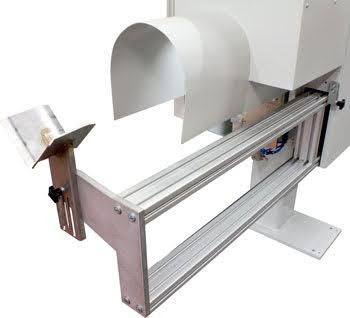
Automatic indexing of blade to extend blade life
The CCA cutting system employs a pneumatically loaded knife. The powerful pneumatic cylinder ensures that the knife will cut through the hard or high resin core materials. For most core materials, the best cut quality is obtained by using a non-rotating blade. The blade is automatically indexed to a new cut position to maximise the life of the blade.
Programmable cut pressure
The cut pressure is set on the touch screen and does not rely on the operator changing a manual regulator.
Dynamic Cut Pressure control
The machine senses the speed of the cut and changes the pressure to keep the speed of cut constant. This Dynamic Cut Pressure system ensures that the cutting time is maintained as the blade ages.
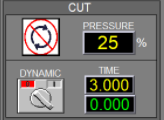
Cut time measurement
The touch screen interface allows cores of different lengths to be programmed in each cut sequence to optimise the usage of the parent cores.
Remote Diagnostic connection and machine commissioning (option)
With this option, we will provide video, telephone and online support for the machine commissioning and training in its operation. Should there be problems, we can also connect remotely to assist in the diagnosis. This connection used a secure high speed broadband connection.
Clean edge cut (without burr)
Some systems use plastic anvils to cut against. These soon become grooved causing a burr to form on the inside of the core. The CCA uses a metal anvil that minimises any grooving and it can be periodically rotated to a new position to maximise its life.
Minimal dust generation
The machine uses a crush cut blade so cutting is achieved without removing material reducing the possibility of dust creation.
60 seconds core size change
The most common size change is from 76mm (3”) to 152mm (6”). The core gripper for 152mm is an adaptor that fits over the 76mm gripper and can be positioned in a few seconds. The cutting anvil is retained with a single bolt and again can be exchanged very quickly.
High speed for large volume core production
Both the cut pressure and the cut time can be optimised for any given core type allowing the maximum production rate.
Core-miser feature to minimise core wastage within current program
Once the core has been measured, the Core-Miser system works out the optimum cut sequence to minimise any waste. A graphical representation of the cut sequence is shown on the display. This is dynamic so you can see the progress of the cutting operation.
Single or multiple cut lengths within same program
The option for variable core lengths is built into the CCA machine as standard. Up to 7 different lengths can be programmed to be cut.
10” high resolution colour touch screen with diagnostics
The large colour touchscreen provides an easy interface for the operator.
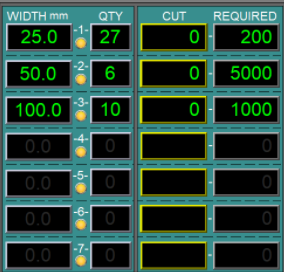
Graphical illustration of planned cuts
When a cut sequence is programmed, a visual representation of the cut sequence is shown on the touchscreen. This is dynamic, changing as each core is cut.

Selector switch for mm and inch
A selector switch allows easy changing from inches to mm for the cut length and core diameter.
Multiple core sizes
The machine can be supplied with a variety of optional core gripping chucks and anvils to suit several ID cores.
Selectable Language
The touch screen has been translated into a number of different languages. This is configured when the machine is ordered.
Automatic core loader (option)
The machine can be supplied with an optional core loading unit to feed the core into the core cutter and to receive the cut cores. A core hopper can also be utilised to feed cores into the core loading unit.
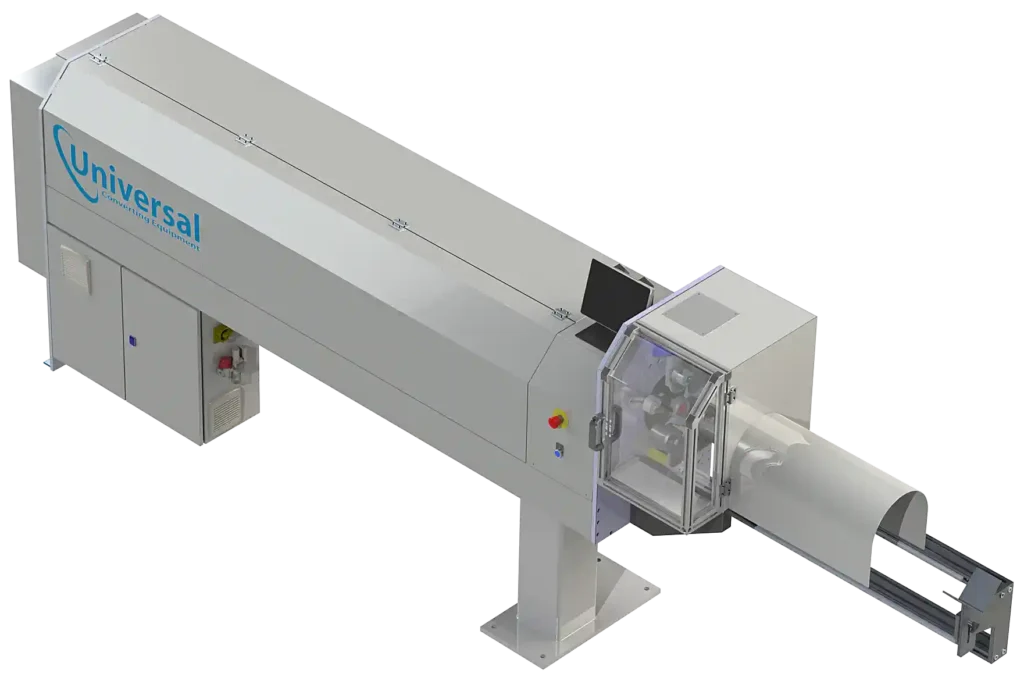
Technical Information | ||
Cutting mandrels available for core ID: | 2 3/4" 3" 4" 5" 6" 6.75" | 70mm 76mm 102mm 127mm 150mm 152mm 167mm |
Maximum core length options: | 86" 137" | 2200mm 3500mm |
Maximum cutting speed: | 60 cores per minute Dependant on core material and cut width |
|
Maximum core wall thickness: | 0.8" | 20mm |
Cut length accuracy: | +/- 0.1mm | |
Minimum: | 1/6 inch | >4mm |
Core material: | Cardboard Paper Plastic |