Following a meeting at K 2022 in Dusseldorf, Bryce Corporation has ordered another two Universal X8 slitting machines from Universal Converting Equipment. The Universal X8 is a highly automated slitting machine. This new order follows on from a major installation of an $8 million Automated Slitting Operation at the Bryce, Searcy, AR, USA facility based on Universal X8 slitting machines.
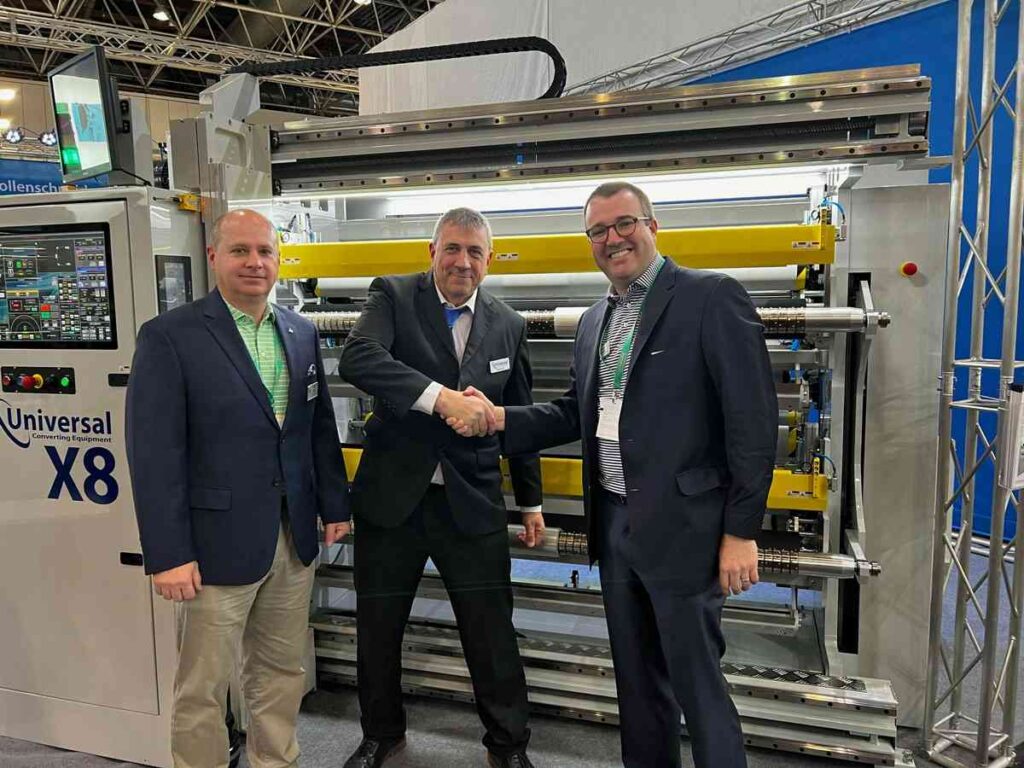
Mike Wilkinson, Sales Executive of Universal Converting Equipment commented, “I have known The Bryce Corporation for over 40 years and have sold them a lot of equipment over that time. The Universal X8 is a unique machine in how technology has been used to overcome problems that have previously prevented higher productivity. It is great to stand and watch the machine producing set after set of finished rolls without an operator present. The Bryce Corporation has a tradition of investing in tomorrow’s technology to stay at the forefront in the flexible food packaging industry. This new order has followed the success of the recently installed automated slitting and roll handling system at Bryce.”
Sean Bowie, President, Bryce Corporation said “The Bryce Corporation is committed to making long-term investment decisions to ensure they have the Best-in-Class processing equipment to cope with the increased demands from our customers. One of the greatest benefits of this system is the reduced amount of manual lifting required by our value stream team members. We have also recently announced the start of building a new factory in Searcy that will employ an additional 142 people. The novel ideas from Universal Converting Equipment fit with our desire to look for next-generation solutions rather than buying the status quo.
This new order follows the recent installation of an Automated Slitting Operation at the Searcy, AR, USA location of Bryce Corporation. Bryce is a major US supplier of flexible food packaging with the capability to serve both the long-run and short-run production orders. Bryce’s previous slitting operation did not meet the needs of their growing markets. They needed machines with automatic set up to allow job changes in a few minutes together with minimal stop time on completion of a set of finished rolls. Most importantly, the slitting machines had to produce high-quality rolls consistently with minimal operator lifting and intervention.
Universal Converting Equipment is a UK-based manufacturer of slitting and rewinding machines. It was established over 25 years ago and has been developing automation systems for slitting machines from the start. The Universal X8 slitting machine is the culmination of that development. Commenting on the X8 development, Alan Jones, Director said “Efficiency is achieved through attention to detail. We keep looking for processes that can be automated to ensure high quality, consistent operation. For example, all our machines include automatic knife positioning of rotary shear knives and razor blades. We have added automatic control of depth and sideloading of shear knives with micrometer feedback to show the operator the exact position and allow adjustment of both critical parameters whilst the machine is running. Optimum knife setting equals high-quality slits and long blade life. All the functions relating to unloading finished rolls and restarting the machines are automated, so the machine runs without an operator at the rewind. The Universal X8 has been a huge development process. Bryce understood the concepts and the thinking behind the systems on the X8 machine and was prepared to invest in machines that did not conform to the old industry standard. They have seen the results of this installation and followed on with a new order for a further two machines.”
The installation and commissioning of the $8 million Automated Slitting Operation have been overseen by Andy Pratt, Vice President of Manufacturing at Bryce plus his team of Engineers. Andy Pratt commented, “We had some very challenging requirements for our new slitting facility involving major improvements in safety, efficiency, and quality. Universal listened and proposed a solution which was different to other suppliers. All the processes relating to unloading, labelling, bagging and palletizing the finished rolls, along with reloading and positioning the cores and restarting the machine are completely automated with this system. We are excited by the efficiency figures being achieved. The ongoing support from Universal has been excellent during the commissioning phase and since we have been in operation.”