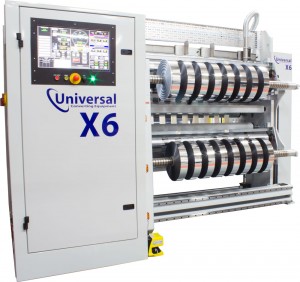
Universal Converting Equipment manufacture class leading slitting machines and other converting equipment that is sold worldwide. The Universal X6 slitter offers a range of technically advanced features to ensure production of high quality product while minimising the amount of time the machine is stopped.
However, to achieve repeat sales, Universal decided they must also offer excellent reliability and customer support. To achieve this, Universal has focussed on four areas within its business:
Designing reliability into the machine.
Our approach is to focus on future reliability as part of our initial design process. We do not make our own drives or circuit boards – we buy our drives from a global supplier with worldwide support.
Our bearings and standard mechanical components are purchased direct from the manufacturer to avoid the risk of supply of counterfeit components. We provide easy access to lubrication points so it is easy to keep components correctly lubricate to prevent premature failure.
Internal manufacture of mechanical components.
Over the last three years, we have invested heavily in CNC machining centres to allow us to make our mechanical components ourselves. This has both improved product quality and reduced our manufacturing lead-time.
As the component drawings now go directly from our 3D CAD/CAM system to the CNC controller there is no risk of data entry error and it ensures repeatability. As part of this process, we have also standardised our components.
Should there be a need for a mechanical component, we will nearly always have it in stock and if not we can make it quickly. We also have extensive stocks of pneumatic and electrical components allowing us to respond to any need for spares quickly.
Comprehensive on-machine diagnostics.
The X6 slitter rewinder can be supplied with a range of automation systems to position the unwind, position the guider sensor, position shear knives and anvils and position the cores.
As the automation grows, so does the complexity of the control system. To make it easy for local engineers to support, we have developed the diagnostic system to give clear reasons if the machine will not operate.
We use a 22 inch colour touch screen as the main operator interface so all the information required can be clearly displayed. If the operator presses the start button and the machine will not start because, for example, a guard is open, a pop up will explain in simple terms what needs to be corrected.
We also provide dynamic electrical circuit drawings which are viewed on the display. They show the status of components such as inputs, outputs, voltages and current meaning that diagnostics which an electrician would do with a meter can be undertaken without even opening the control panel.
Remote diagnostic systems that work.
If we have completed the first three steps correctly then the need for remote support is greatly reduced. Universal is so confident in the reliability of its X6 slitting machine that it offers free telephone and internet based support for the life of the machine.
Sometimes a local engineer can struggle to resolve an issue. All our Universal X6 slitter rewinders have remote access capability via either VPN or port forwarding. The control system has been integrated to a level where when we connect to the machine remotely it is almost the same as being next to the machine. We can see the status of all the control components on the machine and look at the settings on the three touch screens. we can even watch as the operator changes settings on the touch screen.
Instead of the local engineer having to have a laptop with software and interfaces to connect to the machine, we offer this service free to our customers for the life of the machine.
Alan Jones, Managing Director of Universal Converting Equipment adds
“I am always amazed when talking to customers, the number of times I am told that they have purchased equipment that performs well but the ongoing support is poor. Since the launch of our X6 slitting machine, we have seen sales increase rapidly with orders from around the world. Although we will not stop developing the features of the X6 slitter rewinder, our biggest challenge is ensuring that we maintain our reputation for excellent support. Not only are we seeing repeat orders but some customers are ordering two or three machines at a time so the formula appears to be working. We have recently announced a showroom and support centre in the USA which will help consolidate are growing position the the Americas. We always have several X6 slitting machines in build so customers can visit and test their material on a machine. We will also have an X6 slitter rewinder at our showroom in the USA.”